Epoxy, Polyurea & Polyaspartic
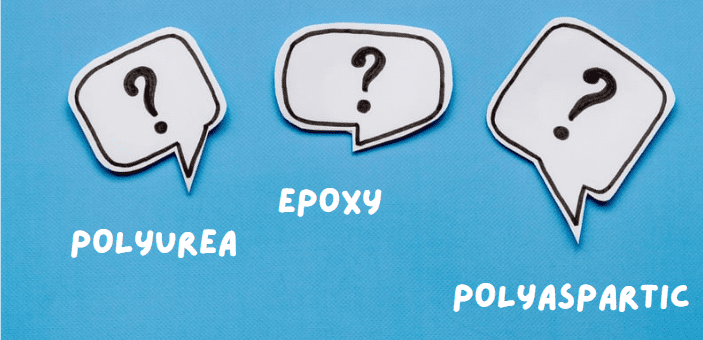
Epoxy, polyurea, and polyaspartic coatings are popular for concrete floors, including garage floors. Each offers unique characteristics and advantages. But how to choose garage floor coatings? Understanding the differences between these coatings can help distributors, contractors, and facility managers make informed decisions based on specific needs and requirements. Epoxy and polyurea are often used for the tinted basecoats in chip flake systems, while polyaspartics are typically chosen for clear topcoats. Polyurethanes and other coatings can also be used as topcoats for garage floors, but this article will focus on explaining the difference between epoxy, polyurea, and polyaspartic technology.
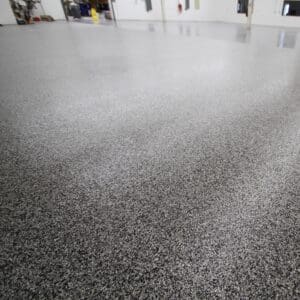
History
- 1930s - The first epoxy resin was developed, and the first polymer was produced.
- 1940s – Epoxy resins gained commercial importance.
- 1970s – Aromatic polyurea became available but remained impractical for use due to rapid cure times.
- 1980s – Companies started using polyureas for floor coatings and auto parts.
- 1990s – Polyaspartic coatings were developed.
Chemical Composition
Epoxy, polyurea, and polyaspartic coatings have two components (“2K”) that require mixing before applying. Once mixed, each product must be applied according to the manufacturer’s recommendations as every product will have different specifications relating to working time, application thickness, and dry time.
Epoxy coatings are typically made from a combination of epoxide resin and a polyamine hardener. The curing process involves a chemical reaction between the resin and hardener, creating a strong and durable surface.
Polyurea, on the other hand, is part of the polyurethane family (but not all polyurethanes are polyurea). Polyurea is formed by the reaction of an aromatic isocyanate component (MDI) with an amine blend. Aromatic isocyanates are deep brown in color and have some odor.
Polyaspartics use aliphatic isocyanates (HDI) as a curing agent. Aliphatic isocyanates are clear and have no odor. However, some manufacturers mix the isocyanate with solvent to aid in the leveling properties and reduce the need to add additional solvent to lower viscosity.
Application Characteristics
Most epoxy coatings are known for their long working times and self-leveling properties. Epoxies are commonly used for decorative flooring applications due to their ability to accept pigment (including metallics), decorative flakes, and quartz. Most epoxy coatings must be poured out of the mixing bucket and onto the floor immediately after mixing. They can then be spread across the floor with a squeegee and/or paint roller before chip flakes are broadcast into them. Epoxies are typically applied at 50 degrees F or higher as they dry quite slowly at colder temperatures.
Polyurea coatings can be formulated to cure much faster than epoxy. They also may be applied in a wider range of temperatures including extreme hot and cold conditions. Like epoxy, most polyurea coatings must be poured onto the floor immediately after mixing. Chip flakes must be broadcast quickly into fast-drying polyureas before they begin to set up and dry. Polyurea coatings are considered “moisture cure,” meaning they require moisture to aid in the curing process. As a result, warm and humid environments will speed up the dry time while cool and dry environments will extend the dry time.
Polyaspartic coatings are typically used as a topcoat for chip flake systems, so contractors often prefer formulas that have great leveling properties and long working times. Polyaspartics may also be pigmented and used on basecoats. They are common for “partial flake” systems where ultraviolet (UV) stability is important. Unlike epoxy and polyurea, polyaspartic coatings do not need to be poured immediately after mixing. They can be poured slowly onto the floor or into a pan and applied with a roller. Like polyureas, polyaspartics are also “moisture cure”, needing some amount of moisture (humidity) to help them dry.
Table 1
Physical Properties and Performance Characteristics
Epoxy coatings are commonly used in commercial, industrial, and residential settings such as warehouses, garages, and manufacturing facilities. Their versatility in formulations makes them a popular choice for many contractors. Epoxy coatings tend to be very hard and rigid. However, when applied as a topcoat, epoxies are prone to yellowing and generally do not exhibit great abrasion resistance. Often, contractors will apply a polyaspartic or urethane topcoat over the epoxy basecoat to increase the overall performance of the system.
Polyurea coatings are highly elastic, flexible, and exhibit excellent adhesion to concrete. They can withstand extreme temperature fluctuations without cracking or peeling. They are often chosen for same-day garage floors or other situations in which a fast return to service is required. Polyurea coatings are typically not UV-stable so they can yellow much like an epoxy. As a result, most contractors use polyurea for basecoats and completely cover them with vinyl chip flakes and/or a polyaspartic coating with UV blocking capabilities.
Polyaspartics are the most common topcoats used in chip-flake garage floor systems. They provide an excellent mix of user-friendliness and performance. Polyaspartics are well-suited for environments where chemical resistance (including tire stain resistance) and durability are crucial. Additionally, the UV-stability of most polyaspartics ensures that they will not yellow when exposed to sunlight.
Cost
Epoxy coatings are usually more cost effective than polyurea coatings. Epoxies offer a durable solution at a lower price point, making them a popular choice for various applications. Aromatic polyurea coatings may have a slightly higher upfront cost but their fast cure times can result in increased efficiency and job cost savings for the contractor. Polyaspartics cost more than epoxies and polyureas but can be formulated in very clear, UV-stable formulas that exhibit excellent abrasion and chemical resistance.
- High-Solids Epoxy: least expensive
- High-Solids Polyurea: generally produced for 25-50% higher cost than epoxy
- High-Solids Polyaspartic: 50-100% higher cost than polyurea
Summary
The choice between epoxy, polyurea, and polyaspartic floor coatings depends on several factors including specific project requirements, desired properties, application conditions, and budget constraints. For a visual comparison of UDT’s product lineup, please to Table 1 above. As you will note, all three coatings have different strengths and weaknesses. Selecting the right one requires choosing a contractor, distributor, or manufacturer that provides high-quality service, consistent products, and clear expectations.
Thanks for sharing the difference between various flooring options here. Before getting any type of epoxy, one needs to understand various types and benefits as well as limitations. Keep sharing.
Matt finish laminate flooring